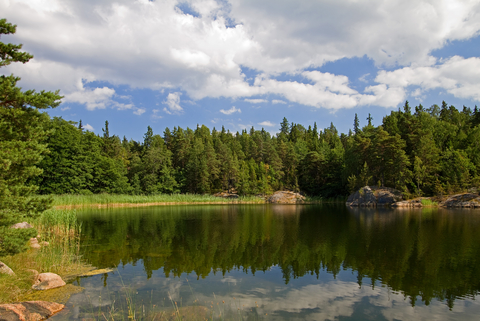
Basi Legani is a unique place – it's the first kosher summer resort to serve the Chicago-area Jewish community. A former campground, it's been upgraded with five brand-new family homes (too comfortable, really, to be called cabins) designed to accommodate several families at a time, if necessary, due to the thoughtful configuration of bed and bathrooms. The old barn now holds a synagogue and learning center on top and a communal kitchen and dining hall on the bottom level, (currently used for a boys summer camp). The presence of the boys, who are just over bar-mitzvah age, ensures a minyan for all visitors. The boys themselves benefit from a scouting-style camp program that is just right for the heavily wooded, slightly mountainous location. A small, private lake allows guests to have fun in the water, and local Amish farmers provide fresh, organic corn, eggs, cow and goat milk.
What more could an observant Jewish family ask for? Well, actually... how
about a mikvah? Not having a kosher mikvah limited the times
that a family could come up to the area. Still, building a mikvah is an
expensive proposition. Once they had decided to do it, the Basi Legani
partners, the Goldbloom and Vile families, wanted to make sure they would do the
job right.
“We wanted to avoid having to re-do anything. We saw many mikvah
facilities that have needed renovations within two or three years. For instance,
one mikvah organization told us they are constantly repairing things:
peeling paint and wallpaper, rebuilding an entire wall because of mold, a
ventilation system that burns out regularly, and so on. We thought, that's
funny, so many other mikvaos we've talked to have similar problems. Why
perpetuate these same issues? We wanted see what might work better than the
standard equipment and construction methods.”
Since the main practical problems seemed to arise from the humidity, the
Basi LeGani planners thought it would be useful to draw on the
experience of hotels and health clubs that have heated indoor pools and spas. In
their research, they found that even many large hotels have had similar
problems, and have had to do major rebuilding and renovation to deal with the
problems of condensation, mold, and excessive chlorine exposure. Finally, they
were fortunate to track down a man who may be the world expert on indoor pool
construction, and hired him as a consultant on their project. “Basically, for a
fee, he spent several hours on the phone with us going over perhaps 20 or 30
important points that made a huge difference in the long-term integrity of our
building,” says Mrs. Goldbloom. Adds Mr. Vile, “Per hour it seemed expensive,
but the information has been so valuable that I have no doubt it was money well
spent.”
Older, European mikvaos were most likely housed in stone or
brick buildings, speculates Mrs. Goldbloom, but modern construction in the U.S.
relies heavily on wood and drywall – materials not designed to withstand
constant, high humidity. Among other instructions, one of the spa expert's
requirements was the use of Duroc-type cement-board for the walls and ceilings –
not drywall. And no Tyvek. He specified a different type of construction fabric
which must be totally sealed – so no vapor can escape the building – to prevent
the winter ice condensation that leads to problems.
The consultant also pointed the Basi Legani team to an indoor
pool specialist, who helped determine the best machinery for the project. One of
the most important requirements was the dehumidifier, imported from England at a
cost of about $12,000. “It was about twice as much as a standard system,” says
Shlomo Vile, “But in our situation it was a must.” They also went with an ozone
water purifier instead of the more traditional chorination, but this only added
about $150 to the cost. A non-chlorine system makes for a more pleasant
experience, and it is easier on the decorative tiles (bromine is still added as
a sanitizer).
One of the main reasons Basi LeGani has insisted on
top-of-the-line equipment is the nature of their facility. Although some
families drive up for fall and winter vacations, most come during the summer.
Weeks and even months can pass without anyone checking on the mikvah machinery.
A mechanical problem that would be noticed right away in another location could
go a long time without remedy at Basi LeGani, where the equipment is
running constantly. “We needed something that would be so reliable it could
almost be automatic,” says Vile.
The dehumidifier doubles as a heating system, although a secondary heat
source was also installed. They could have used forced-air or radiators, and but
they chose an in-floor radiant heat system. “That was definitely a luxury
option,” admits Vile. But it's in keeping with the overall plan of the
mikvah – which also sports a sauna, a massage room, an up-scale bidet,
and a high-tech bath/shower enclosure with a built-in whirlpool.
Adding to the posh feeling is the carefully-planned decor -- celestial
blue Carrera marble for the walls of the mikvah inset with a matching
chair-rail height mosaic. The floor is a blue-and-white basket-weave tile, which
adds further texture without seeming busy. “Blue is a calming color, and of
course it evokes water,” says Mrs. Goldbloom. That blue is picked up in every
room, in the glossy blue-green marble floor tiles throughout the
mikvah, and even in the antique stained-glass windows in the interior
mikvah corridor, painted with a blue and brown nature motif.
The entire project took about a year, from conception to completion, and
cost about $100,000, not including the sauna. Rabbi Gershon Grossbaum,
acknowledged international mikvah expert, came to inspect the site in the summer
of 2006, and the foundation for the building was poured that November. By the
summer of 2007, the facility was completed and in full use.
Any snags? “We had about the same issues that you might expect with any
involved construction project,” says Vile, “although for a mikvah the
stakes are always higher, because a major mistake makes the difference between
kosher or not. Thank G-d we didn't have any serious problems, although there was
a small technical glitch when the cement sealant wasn't applied at the right
time. We had frequent rabbinical supervision during the construction, which
wasn't easy, since we're more than four hours away from where the rabbis are.”
Vile, an engineer by training, also says he would have liked to have had more
time to understand the mikvah requirements, so he could be a better liaison
between the rabbis and the builders. “Our builder, who is quite good, told us
that this was by far the most complicated project he's every worked on.”